THUNDER BAY – Many have called the efforts to combat the Coronavirus Pandemic a war on the virus. Perhaps then it is very fitting that at the Bombardier manufacturing plant in Thunder Bay is making ventilators to be used to win this war and save lives.
Helton Santos, Vice President, Sales and Marketing, 0-Two Medical Technologies says, “Our North American supply chain is now up and running! It took some time and we appreciate how hard the team is working at Bombardier’s Thunder Bay plant, along with all of our suppliers, to make sure we meet our commitment to producing these life-saving ventilators for the Province of Ontario.”
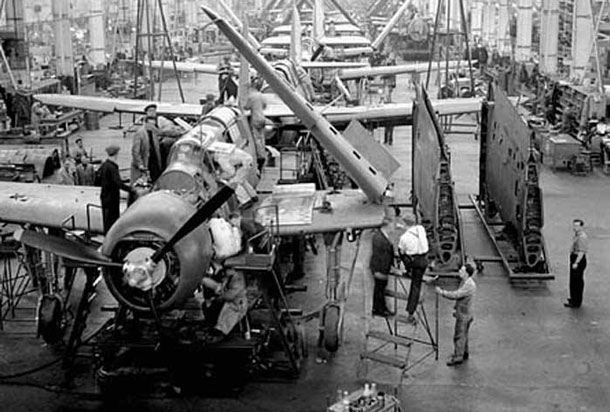
“We are very proud to be able to produce these medical devices which can aid in the fight against this pandemic. The Thunder Bay team are highly skilled and highly motivated to do their part in supplying these ventilators. Over the years, this site has produced various products from minesweepers in WWI and Hawker Hurricanes in WWII to busses and various rail transportation products. These ventilators may be the smallest product we have ever produced but equally as important,” says Dave Black, General Manager, Thunder Bay Bombardier Transportation.
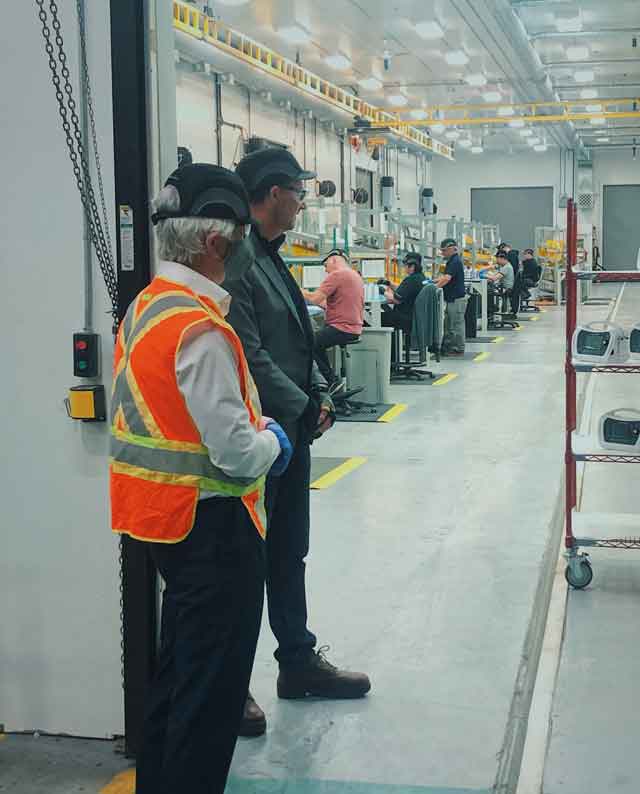
The Bombardier Transportation Thunder Bay Plant has been, for the past year and a half been scaling down activity and laying off workers due to the lack of projects in the transportation pipeline. The employment level, once at 1,100, is now hovering around 470. The search, internally and externally, for projects to achieve critical mass remains a top priority.
With the arrival of COVID-19, Bombardier’s leadership and employees knew they wanted to help flatten the curve of COVID-19. After making sure Bombardier employees are protected in their jobs, the company looked to make a difference in fighting the pandemic. The company (Aviation and Transportation) donated surplus PPE to Ontario Long-Term Care facilities and the Quebec Government, manufactured face masks that were approved by Health Canada and purchased by the Quebec Government, produced masks that were purchased by the Government of Quebec and donated a plane to deliver PPE to Nova Scotia in support of Conquer COVID.
In Thunder Bay, thanks go to the Thunder Bay-Rainy River federal MP, Dr. Marcus Powlowski, who connected the local Bombardier Transportation plant’s General Manager, Dave Black, with Helton Santos, the Vice President of Sales and Marketing of 0_Two Medical Technologies (a company that makes ventilators, located in Brampton, Ontario). 0_Two’s supply chain was completely disrupted by COVID-19 and they needed to secure help in Canada to manufacture their portable ventilators.
Marcus Powlowski, Federal M.P., Thunder Bay-Rainy River comments, “Today is a great day for the Thunder Bay plant. These are some of the first ventilators that have been ordered in Canada in response to the COVID-19 pandemic to be built. This is a testament to the skill and talent of the plant’s workers and shows all of Canada the importance of keeping the plant operational.”
Bombardier leveraged both business units – Aviation and Transportation – to come up with a production process to do the work 0_Two needed to supply e700 ventilators to the Ontario Government.
After several collaborative discussions and gaining a full understanding of what was needed to produce these life-saving devices, it was clear that Bombardier’s plant in Thunder Bay could play a sub-manufacturing role and help 0_Two produce this critical medical equipment. The full production line is now in operation.
Dom Pasqualino, President Unifor Local 1075 states, “Unifor Local 1075 appreciates the opportunity to be a part of the solution to the COVID-19 crisis. Our highly skilled and versatile workforce have quickly adapted to manufacture the smallest product the plant has ever produced in its 100-year history. Our team is dedicated to doing everything possible to support the hardworking frontline healthcare workers”.
Bombardier Key Points
- In addition to getting ourselves organized, for the past two weeks we have been manufacturing different components that make up the full casing for the ventilators. Today we are announcing that we are in full production mode.
- We appreciate the work of our local MP to connect us to 0-Two.
- There is work on this production line for 50-60 employees for 3 to 4 months. We were able to call back about 45 employees. The rest are employees for this project are active now at the plant.
- We are a proud Canadian-based company and we are motivated to contribute to help flatten the curve of Covid-19.
BACKGROUND:
What’s been happening since April 16th when you announced that Bombardier’s Thunder Bay Plant was tapped to be a sub-manufacturer to 0_Two?
- prepared and set up a “clean room” where the production line – that has eight stations – is running
- conducted training, and prep work to understand and formulate appropriate production procedures
- established health and safety protocols for this new production line
- manufactured parts for pre-approval by the customer
- assembled various components so the line could be ready for the final step of assembly
What is your scope of work? What are employees doing?
- finishing of the housing components including sanding and prep for paint
- painting and electrical resistance testing of the paint
- Assembly of the internal working components including items such as the display screens and battery box installation
- Electrical conductivity testing
- QA inspection
- Packaging and shipping to O2 who will do a final assembly and test the completed unit
What are you announce?
Today we are announcing that we are in full production. We had to design our production line, get it set up, manufacturing various parts for pre-approval from the customer as well as other components along with receiving shipments of material from the customer. We look forward to providing timely updates on our completion numbers.
We heard the delay was caused because you were missing parts from O_Two – can you confirm?
0_Two Medical Technologies had its supply chain completely disrupted by COVID-19. They needed to secure help in Canada to manufacture their portable ventilators. We were grateful for the support provided by our local MP in connecting us with 0_Two. We leveraged both of Bombardier’s business units – Aviation and Transportation – to come up with the materials needed to create a production process to do the work 0_Two needed to supply e700 ventilators for the Ontario Government. They faced some challenges to be sure. What matters is that today we announced we are full production.
Will this be a new business for Bombardier Transportation?
We are proud to support efforts to manufacture domestically medical devices, by leveraging our engineering and manufacturing expertise. We strongly believe that supporting and developing local manufacturing capabilities, while engaging in international trade and business, is important for Canada’s economic security and prosperity, as Premier Ford and the Ontario government have stated.
Our core business remains the manufacturing of large transportation equipment, i.e. commuter trains, subways, and light rail vehicles that are considered critical infrastructure and essential services in Canada and around the world, and our intention is to continue to do so by keeping our plant commercially viable. We are doing everything possible to have this critical expertise in Thunder Bay fully recognized and leveraged in Canada. When we are at critical mass, we use almost all the square footage at the plant.